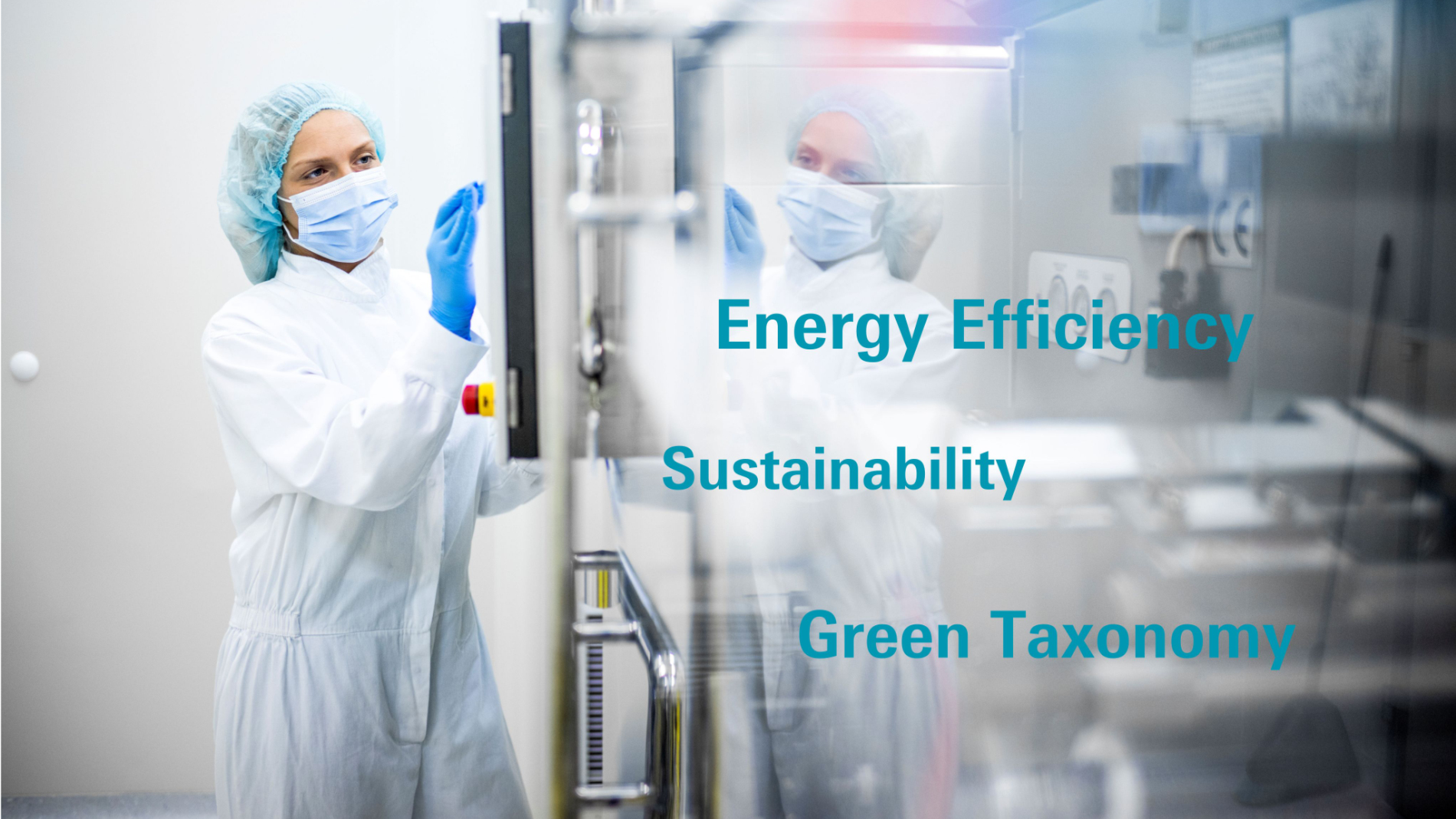
July 2024
With wars and other crises around the globe, energy supplies appear to be heading towards a future characterised by uncertainty or higher costs – or both.
There is also a need to reduce carbon footprints and continue lowering greenhouse gas emissions. These imperatives can be seen in the European Green Deal, which calls for climate neutrality by 2050. The EU Taxonomy Regulation supplies the technical framework. The aim is to make it possible to measure the degree to which an investment is ecologically sustainable. This is combined with disclosure obligations that require companies to reveal their ‘non-financial’ ecological and sustainability efforts.
All of these factors are forcing companies to save energy. But can this really be done in cleanrooms?
Ideas for energy efficiency with a multiplier effect
First and foremost, a cleanroom must be just that – clean. Energy efficiency can only be of secondary importance here. Before the 2000s, people gave little thought to energy costs, but instead focused on achieving the level of purity necessary for the process. Yet conditioning and purifying air in particular is energy-intensive, and this continues to grow more expensive. As a result, the past twenty years have seen this process change from an always-available commodity to a cost-critical factor.
Today people are paying far closer attention to energy efficiency, and one reason is that they are more aware of its importance to the bottom line. For example, a full 60 percent of the Fraunhofer Society’s energy costs are accounted for by its cleanrooms. The good thing about this: energy saving ideas should result in large multiplier effects, and the Fraunhofer Society is already working to take advantage of this potential.
There is also a lot going on at the Association of German Engineers (VDI), where a working group is currently developing a new set of guidelines for energy efficiency. They are revising the guideline VDI 2083 Sheet 4.2 “Cleanroom technology – Energy efficiency”, which has been around since 2011 (and is therefore no longer entirely up to date).
Everyone with an interest in this process has a seat at the table, in particular those involved in planning, building and operating cleanroom facilities, representatives of research and education institutes, and manufacturers of measurement and control technology and cleanroom components.
Thomas Wollstein, who is serving as a research consultant in this VDI working group, is happy with the progress being made: “We hope that we will soon be able to issue the new guidelines.” As to the content, he can already reveal that ‘Cleanroom and ventilation concepts’ and ‘Energy-efficient operation’ are the new guidelines’ two biggest areas of focus. The following topics have also been given special treatment: ‘Energy requirements of cleanrooms’, ‘Energy-relevant parameters and special features of cleanrooms’, ‘Process for assessing and increasing energy efficiency’, ‘User and planning requirements’, ‘Commissioning’ and ‘Optimising operation in terms of energy consumption’.
The new components of VDI 2083 are frequently similar to the corresponding sessions of the DIN EN ISO 14644 standard, and this should come as no surprise, because VDI working groups are generally participants in global committees, so their requirements have international significance.
Implementation of guidelines and recommendations in actual practice
Anyone who is aware of the topic of ‘energy efficiency in cleanrooms’ quickly recognises numerous areas in which this is relevant. One example: rather than operating a cleanroom 24 hours a day for seven days a week at the highest air exchange rate, it should only be run when production is in progress. There are also always various ways in which particular air qualities and purities can be achieved – ways that require differing amounts of energy. Heating and ventilation technology are often the first ports of call. And in keeping with the rule that the most cost-effective cleanroom is one that does not need to be built, it is important to ask the following questions whenever such a new build is planned: Do I need a high-level cleanroom, or would a less stringently controlled environment be sufficient?
With an existing cleanroom, optimising energy consumption requires a strategic approach. Should the operator take a four-point approach, for example, they must ask themselves the following questions:
Question 1: Can I replace the existing filters with better ones?
Question 2: Does my cleanroom already have possibilities for heat recovery?
Question 3: To what degree might it be possible to reduce the number of air changes per hour?
Question 4: What can be done to improve the efficiency of motors and/or drive systems?
The key when asking these questions is to be open to any possible answer. It is time to mothball the old rules of thumb, such as 20 air changes per hour and 30 percent external air being the absolute minimum that is required.
Ventilation is a key area in which changes can be made. In particular, air that has been drawn into the cleanroom and fully filtered should never be pumped straight back out again. Instead, any air that has already been treated should remain in the cleanroom and then be circulated. There are practical fan filter units (FFU) available for this very purpose. These continuously clean the air and feed in oxygen-rich air from outside. It is also generally the case that ventilation concepts are the most important factor for maximising energy efficiency in cleanrooms.
Tolerances are another area where changes can deliver benefits. Some cleanroom operators defined tolerances when they started operation without giving thought to optimising their energy efficiency. Should the product being produced be able to cope with moisture levels of anywhere between 20 percent and 80 percent, there is simply no need to require stricter tolerances. And if it is possible to change the temperature requirements from 21 °C (± 1 °C) to 21 °C (± 3 °C), this promises further energy savings. If external and internal temperatures are the same, it might even be possible to switch to ambient cooling and (at least temporarily) do without the entire energy-intensive cooling system.
On 25 and 26 September 2024 in Frankfurt am Main, Cleanzone will be showcasing strategic approaches to increasing energy efficiency in cleanrooms, as well as state-of-the-art products that are suitable for this purpose.
Tags
- Trade Show