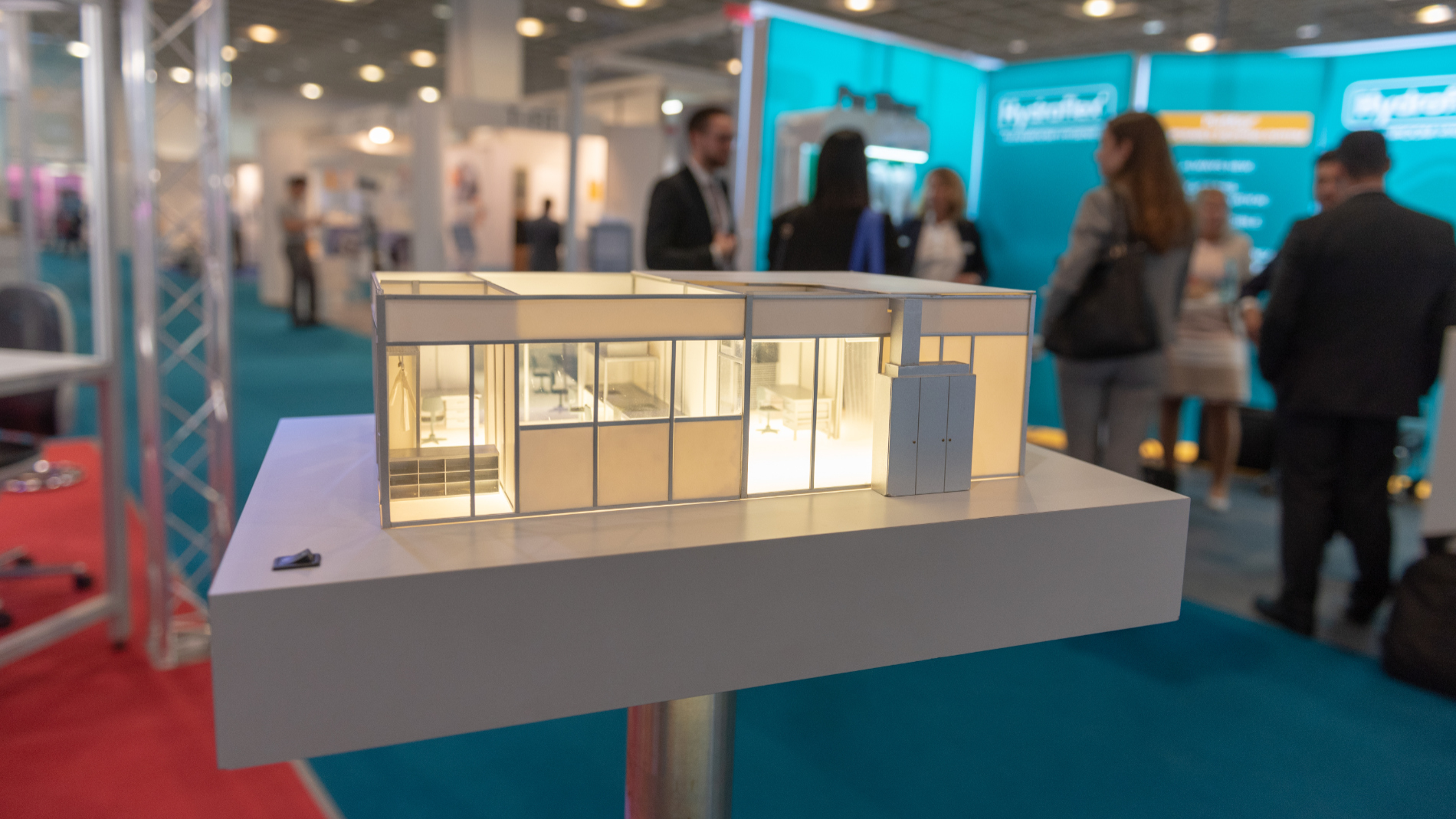
The Ukraine conflict, tensions in the Middle and Far East, economic embargoes - all these factors contribute to the increase in the cost and scarcity of energy. This affects many companies and cleanroom operators in particular. Because air circulation and temperature control eat up energy. That is why the demands on cleanroom specialists are increasing: Where are the opportunities for savings?
The order of the day: Investment in technical cleanroom infrastructure
This question naturally causes unease, especially in the sensitive areas of pharmaceuticals and life sciences, where occupational health and safety and the safety of processes are of paramount importance. But in the entire industry, not only has interest in energy saving and CO2 footprint reduction increased in recent years, but recently also the willingness to invest. Today, optimisation measures in this area do not have to fail because of fundamental concerns or profitability considerations. On the contrary: even unconventional suggestions from cleanroom specialists are welcome. The industry is investing wisely in technical infrastructure and no longer expects to achieve the targeted return on investment (ROI) within a little more than a year. Instead, more often up to three and a half years are set.
But where is the greatest potential for savings in the "pharmaceutical and life sciences" sector? The main findings can be formulated as follows: 90 per cent of all cleanrooms are ventilated turbulently, and almost always the air exchange rate is oversized. A current example may illustrate this:
Reducing air exchange in a sterile production facility
In the sterile production of a pharmaceutical manufacturer, the air for a cleanroom area of 7,600 square metres is filtered, heated, cooled, humidified and dehumidified with turbulent ventilation. In particular, a hot air sterile tunnel is operated in one of the clean rooms. A large part of the control is handled by several HVAC (heating, ventilation, air conditioning) systems. The focus of the energy reduction considerations is the question: Can't the volume of cleanroom air exchanged per hour also be smaller without endangering operation in accordance with regulations?
To determine the savings potential, cleanroom experts first compare the air exchange rate at the current level with the air exchange rate required for sterile production. In doing so, they also take fixtures into account. For although the cleanroom area is specified at 7,600 square metres, the cleanroom volume is reduced, for example by 1.6 m² due to a closed cabinet measuring 1 m x 80 cm x 2 m. Consequently, the supply air volume may also be reduced accordingly. Recirculation units with HEPA filters and areas with low-turbulence displacement flow are also taken into account - in short: all units from which air overflows into the cleanroom. Caution: These installations are by no means lowered themselves. But the extent to which they contribute to the air change is included in the total cleanroom air change rate. Up to this point, only a potential saving has been determined. In this specific case, we are talking about a possible saving of supply air in class D cleanrooms of about 104,000 cubic metres per hour - almost a third (31 %). The following must always be taken into account for the possible cost reduction: air change reduction always also means that the fresh air flow can be reduced. This means additional savings in thermal energy for heating, cooling, humidifying and dehumidifying. In the example presented here, the theoretically possible savings for all HVAC systems considered result in a supply air volume flow reduction of 99,800 square metres per hour. Initially, the operator realised 13,000 of these by converting two HVAC systems. The result is an energy saving of 24 per cent (HVAC No. 1) and 31 per cent (HVAC No. 2), an energy cost reduction of 60,000 euros per year and a CO2 emission reduction of 24 tonnes per year. Also more generally for existing cleanrooms, where 100 per cent outside air systems are used, there is often the option of converting them to recirculation systems. Of course, risks such as cross-contamination may have to be eliminated in a different way than before. Any change to the existing cleanroom technology must be assessed for its impact on the critical GMP parameters. It is a balancing of risks and benefits, and for this the operator needs cleanroom experts.
Besides ventilation technology, it is often humidity management that leads to unnecessary energy consumption. The right counter-strategy: Instead of focusing primarily on the cleanroom and its specifications, one should ask what the decisive conditions are for the product quality (e.g. for an active pharmaceutical ingredient). After all, the product may have a greater tolerance to moisture than the cleanroom standards and recommendations originally compiled would have suggested. This then opens up new scope for reducing energy consumption. In general, another possibility for saving energy is always heat recovery.
Correct planning right from the start
Existing cleanrooms can be optimised in terms of energy and costs by redimensioning. This automatically leads to the question: why not pay attention to the right design from the very beginning?
The tools available for this have recently expanded. One of them is called BIM, Building Information Modelling. It brings all the trades together digitally in the planning phase, for example in a cloud. The more intensive communication between all parties involved pays off in faster completion, in energy- and cost-optimised operation right from the start, and in further savings effects in facility management over the entire duration of management. A "digital twin" of the cleanroom facility, which is created during the planning phase, can also be used later to realise conversions and other changes quickly and cost-effectively. The recommendations of the Association of German Engineers for the Cleanroom (VDI 2552) ensure an open standard for BIM projects - open in approach, sufficiently standardised for reliable results. In addition, according to the motto "The best cleanroom is the one I don't need": always consider first whether larger machines and equipment belong in the pharmaceutical or biotech cleanroom at all. Because often the better way is to move the decisive action into mini-environments, small, fully robotised cleanrooms, and to group supply, removal, etc. around them.
A good opportunity to find out about the opportunities for cost-saving and sustainable operation of cleanrooms is offered by the Cleanzone trade fair on 23 and 24 November 2022 in Frankfurt am Main. Innovative companies from this sector will present promising concepts for the efficiency of pharmaceutical and biotech cleanrooms in lectures and panel discussions - a magnet for visitors.
Cleanzone
International trade fair for cleanroom and cleanliness technology, hygiene and contamination control.
Cleanzone will take place on 23 + 24 November 2022 in Frankfurt am Main.
+++ Online Press Accreditation +++
The online press accreditation for Cleanzone 2022 is now available:
https://pressaccreditation.messefrankfurt.com
Due to a system change, please note the following information:
- The previous login data for the Messe Frankfurt accreditation tool (before 2021) is no longer valid.
- If you already have a Messe Frankfurt login, please use this access data to register.
- We would like to ask you to update or complete your profile at this time.
- If you are registering online for the first time and do not yet have an account, simply go through the registration process step by step.
In case of any further question, please contact press.cleanzone@messefrankfurt.com
Further information on the top themes at Cleanzone: www.cleanzone.messefrankfurt.com/top-themes
Further information on the Cleanzone Conference: www.cleanzone.messefrankfurt.com/conference
Further information on Cleanzone: www.cleanzone.messefrankfurt.com
Follow us!
www.cleanzone.messefrankfurt.com/facebook
www.cleanzone.messefrankfurt.com/twitter
www.cleanzone.messefrankfurt.com/linkedin
Background information on Messe Frankfurt
The Messe Frankfurt Group is one of the world’s leading trade fair, congress and event organisers with their own exhibition grounds. With a workforce of 2,200 people at its headquarters in Frankfurt am Main and in 28 subsidiaries, it organises events around the world. As in the previous year, annual sales for 2021 were significantly lower owing to the COVID-19 pandemic: approximately €154 million compared with Group sales as high as €736 million in pre-pandemic 2019. We serve our customers’ business interests efficiently within the framework of our Fairs & Events, Locations and Services business fields. Sustainable business practices are a central pillar in our corporate strategy and strike a healthy balance between ecological and economic interests, social responsibility and diversity. Another of Messe Frankfurt’s strengths is its powerful and closely knit global sales network, which covers around 180 countries in all regions of the world. Our comprehensive range of services – both onsite and online – ensures that customers worldwide enjoy consistently high quality and flexibility when planning, organising and running their events. We are using our digital expertise to develop new business models. The wide range of services includes renting exhibition grounds, trade fair construction and marketing, personnel and food services.
With its headquarters in Frankfurt am Main, the company is owned by the City of Frankfurt (60 percent) and the State of Hesse (40 percent).
For more information, please visit our website at: www.messefrankfurt.com
